We’re not just about transforming materials.
We’re about transforming processing itself.
Processing is the foundation on which the world is built. But the world is changing, fast. And processing must change, too.
We innovate to make material processing more circular - using ingenuity and digital solutions to help you find the sustainability and efficiency your business - and the world - needs.
countries of installed bases
tested materials
technical experts
patents
Across markets.
Across the globe.
We operate globally, through a network of companies in 12 countries around the world, partnering with major players in the Infrastructure, Energy, Chemicals and Performance Materials sectors. A global technology provider, leading the way with precision, accuracy and premium quality in material processing.
140 years of innovation.
At your disposal.
With 140 years engineering experience and 300 patents to our name, we lead the way in measuring, combining and processing technologies. By building trusted relationships, our experts apply a responsive and flexible culture to put all our know-how into transforming your processing.
Dr. Ulrich
CEO Schenck Process
“Industrial processing is fundamental to industry, and innovation is fundamental to Schenck Process. We’re driven
by experience and ingenuity to keep making the transformation of materials more accurate, more efficient and more
sustainable.”
Our Senior Leadership Team
Meet the leaders who guide our passion for solving complex challenges – and empower us to deliver continuous improvement in everything we do.
Dr. Jörg Ulrich
Chief Executive Officer
Dirk Scholz
Chief Financial Officer
Peter Groll
Chief Technology Officer
Manfred Bruckner
Managing Director EMEA
Rajesh Pathak
Managing Director India
Benjamin Weber
Managing Director China
We know our material. And yours.
Since 1881, we’ve worked with all kinds of enterprises, using all kinds of materials. It’s this deep knowledge of material properties, across a spectrum of bulk materials, that gives us invaluable insight into solving your mission-critical applications.
Our experts.
Dedicated to your challenges.
Innovation happens with over 1,100 Schenck Process people dedicated to solving your processing problems - and supporting you to implement the solutions. Globally, tirelessly.
- 125 local technicians on call
- 24/7, 365 support
- 24 local service hubs
Increasing your efficiency.
Reducing your downtime.
Sustainability means looking for efficiency. We find it with innovations in processing technology and methodology. Giving you more accuracy, consuming less energy, using fewer resources and incurring less downtime.
- 99.5% feeding accuracy
- 80% downtime reduction
- 20% energy savings
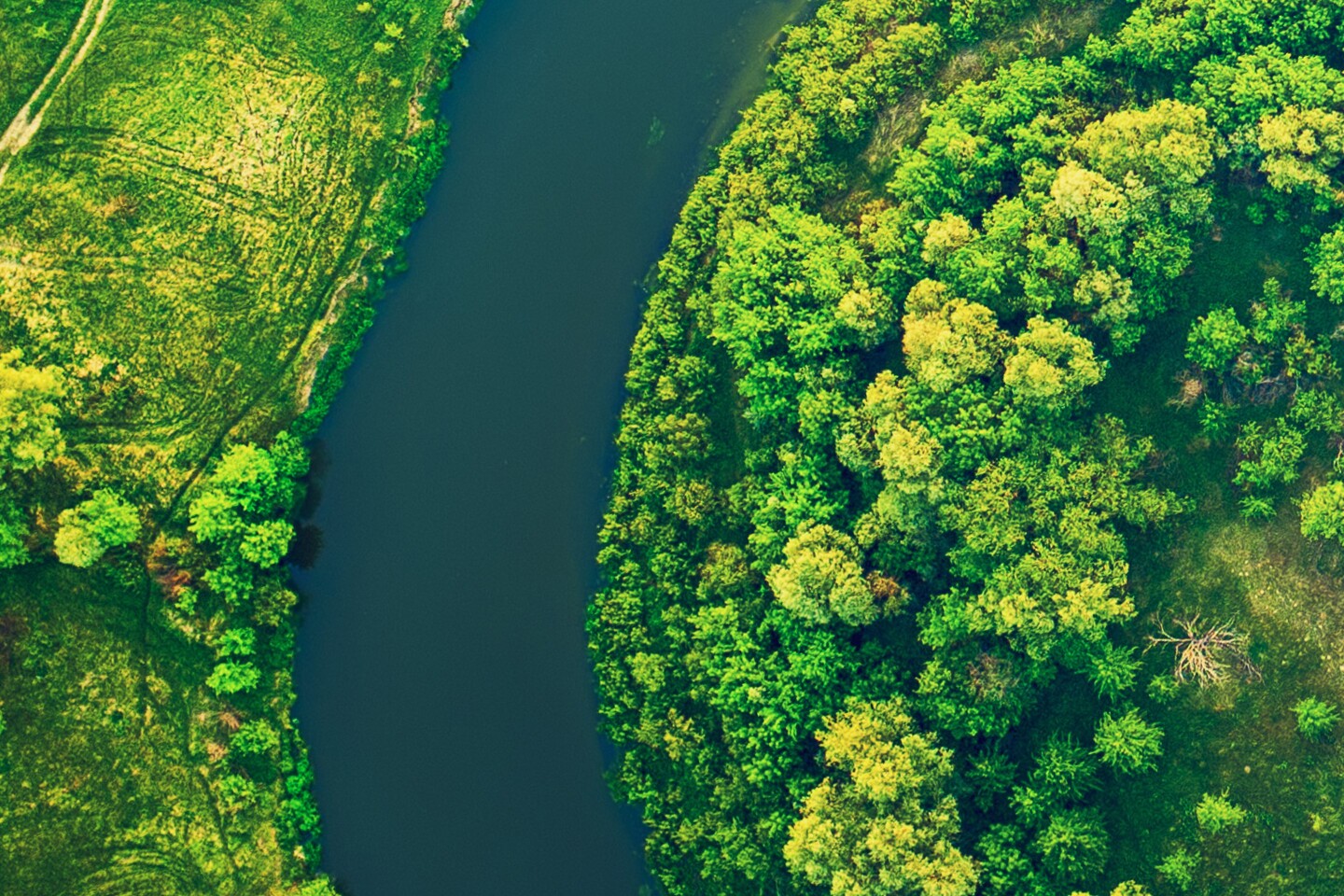
Resources are finite.
Our ingenuity isn’t.
Unlike raw materials, our determination to find better solutions is endless. Our mission to develop sustainable new technologies can help you towards Net Zero, and reduce the amount of resources you need. Or even replace them entirely.
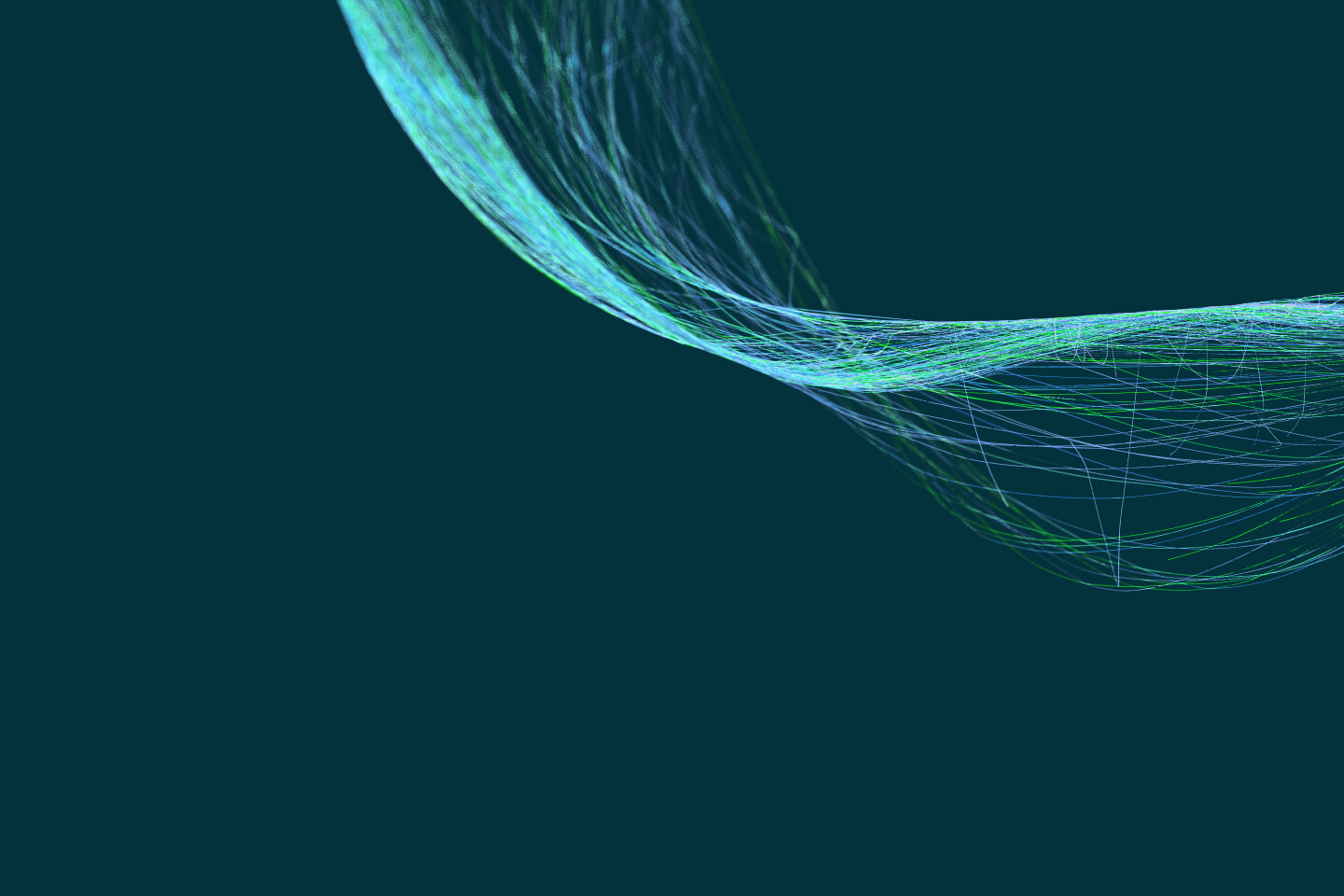
Harnessing data.
Powering insight.
Data is a super power that enhances processes. Cloud-based, it becomes accessible to all. Monitoring and actioning KPI metrics from mobile devices. Feeding algorithms that pin-point improvements and anticipate issues. We capture it, harness it, and put it to work.
Challenges.
We process them.
Solving complex processing problems is our lifeblood. It's the driving force that fuels all aspects of how we work with you to deliver more efficient, more sustainable processing solutions.
In a world that is becoming more dynamic, digital and complex, we set out not just to transform materials, but processing itself.
Let’s do it - together.
We’re there for you
Partnership for us means always being on hand to support you whenever and wherever you need us. With our global network of locations and expert partners, we make sure we are always right by your side.